Prépolissage, polissage et gravure de pièces fabriquées par additif
Les étapes de préparation du prépolissage, du polissage et de l’attaque varient considérablement en fonction du matériau/alliage lorsque l’on travaille avec des échantillons fabriqués par additif. Voici de brèves recommandations pour quatre matériaux courants utilisés en FA.
Titane En général, la préparation doit suivre les méthodes standard utilisées pour les autres échantillons de titane.
- En raison de sa ductilité élevée, le titane est sujet à la déformation mécanique et aux rayures. Le polissage diamanté doit être évité, en particulier avec du titane pur.
- Pour le titane moins allié, il est recommandé d’effectuer un électropolissage.
- Pour révéler plus d’informations, l’attaque est souvent nécessaire après une préparation mécanique ou électrolytique. Comme le titane est résistant aux produits chimiques, il est recommandé d’utiliser des réactifs d’attaque contenant de l’acide fluorhydrique.
- La lumière polarisée est une excellente méthode d’attaque optique pour le titane.
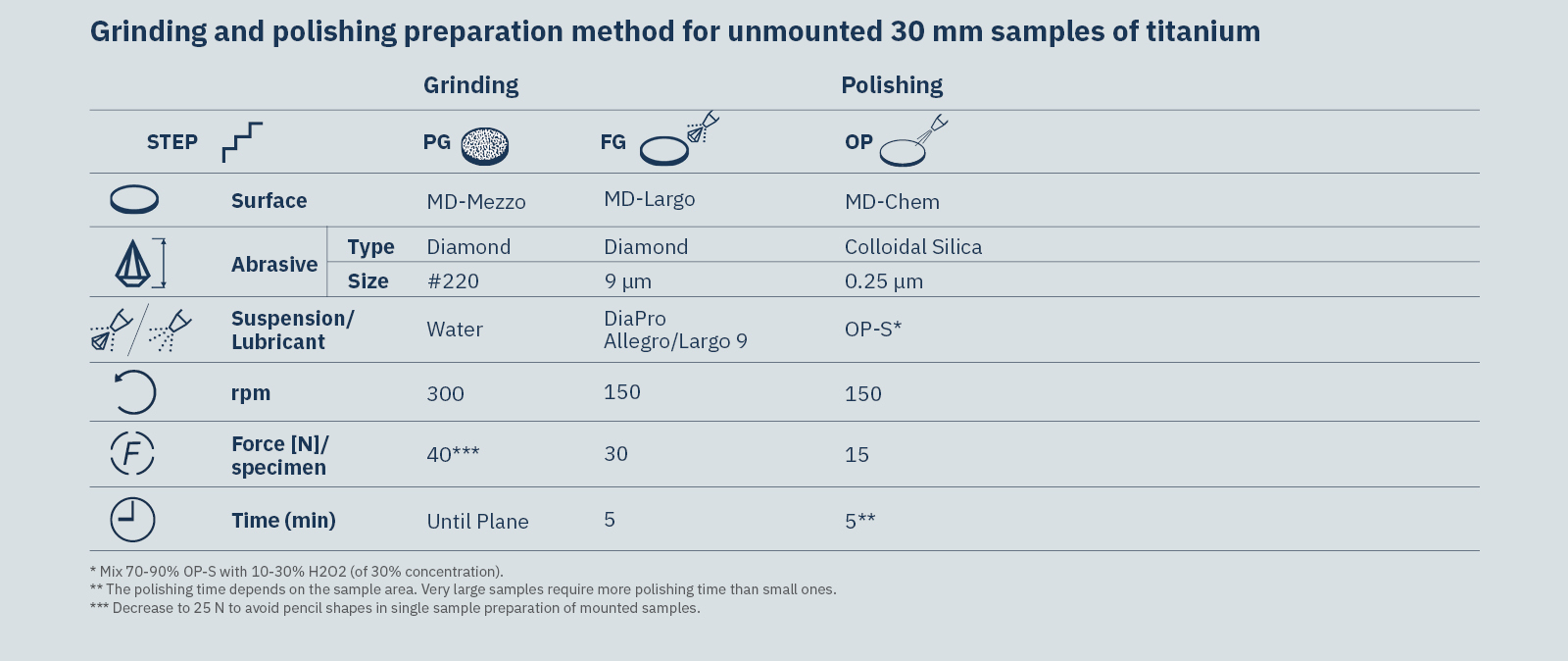
Tableau 2. Méthodes de préparation de prépolissage et de polissage pour échantillons de titane de 30 mm sans extraction de l'enrobage de son moule.
Voir la note d’application complète pour des descriptions détaillées et des méthodes éprouvées de polissage, d’électropolissage et d’attaque d’échantillons fabriqués avec de l’additif au titane.
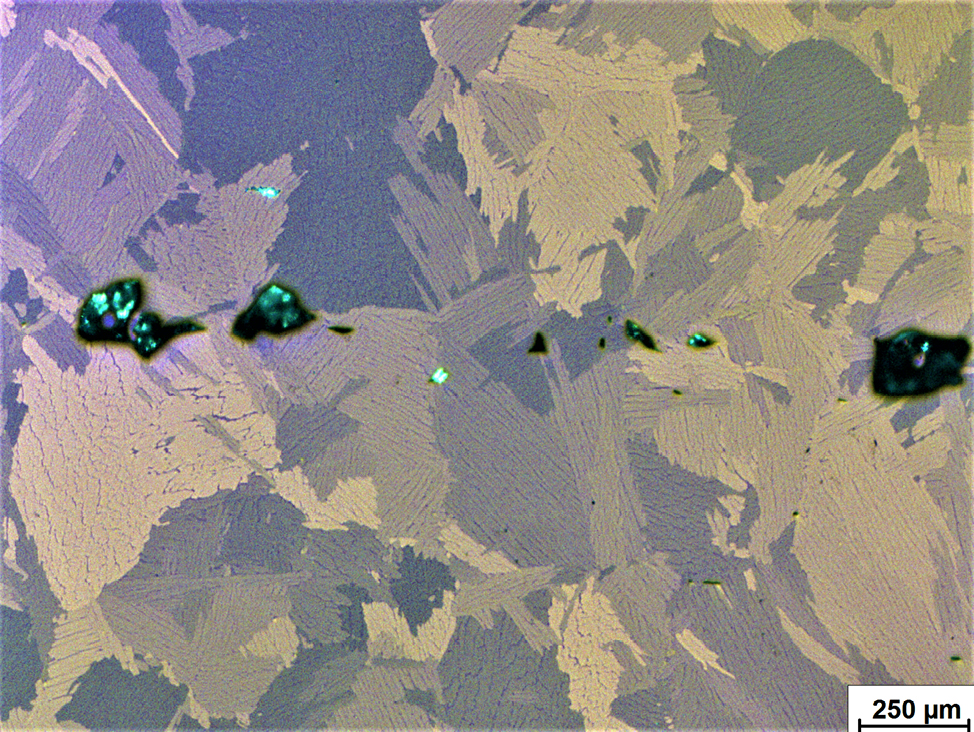
Figure 14. Échantillon de titane avec polissage final et pores. Polissage sur drap MD-Chem avec OP-S NonDry et additif, avec contraste de polarisation.
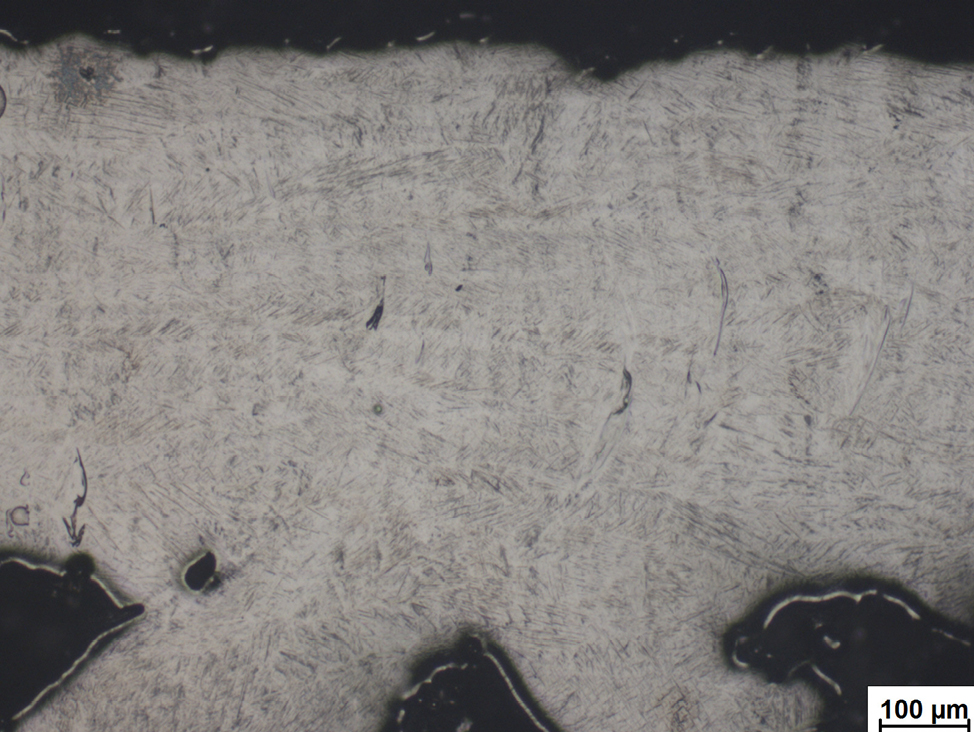
Figure 15. Alliages de titane Préparation électrolytique avec A3, en fonc clair sans enrobage. Fond clair.

Figure 16. Alliages de titane Alliage en titane par polissage électrolytique et attaque chimique avec réactif de Fuss. Fond clair.
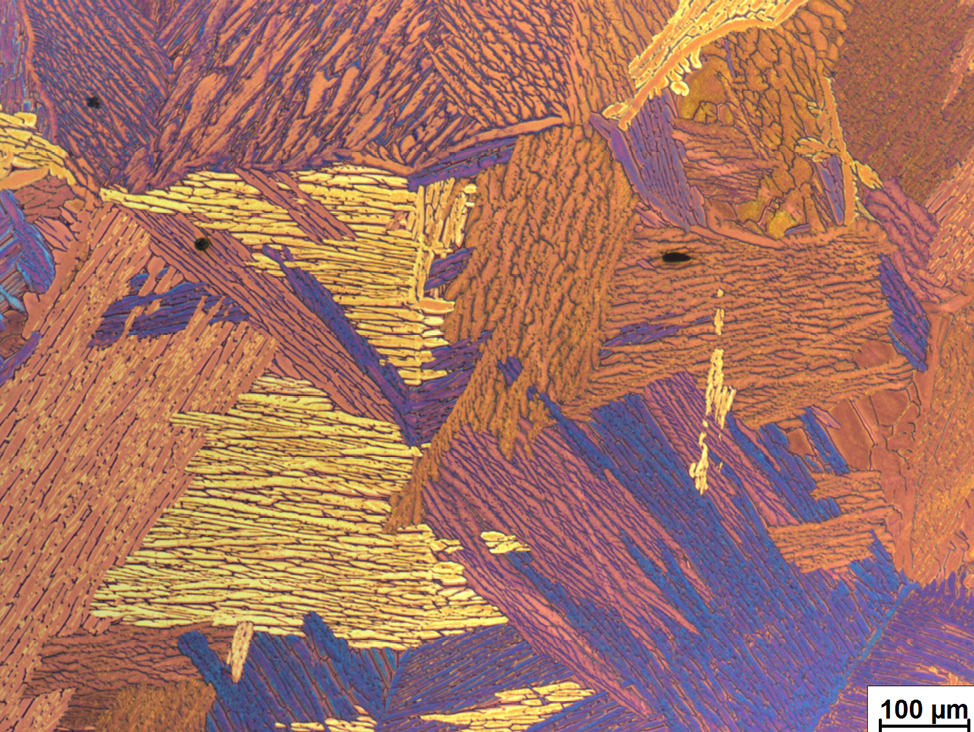
Figure 17. Alliage en titane après attaque avec réactif de Keller. Lumière polarisée.
Aluminium Bien que l’aluminium soit tendre, les éléments d’alliage peuvent considérablement modifier ses propriétés mécaniques. En général, la préparation d’échantillons fabriqués par additif doit suivre les méthodes utilisées pour des échantillons d’aluminium similaires.
- Pour éviter les déformations, les rayures et l’arrondi des bords, il est recommandé d’utiliser un support de prépolissage plan rigide spécialement conçu pour les alliages d’aluminium, appelé MD-Molto.
- Lors du prépolissage fin, MD-Largo avec suspension diamantée (p. ex. DiaPro Allegro/Largo) convient à de nombreux types d’aluminium.
- Pour garantir un polissage complet, suivez les étapes de prépolissage fin avec un polissage diamanté (MD-Mol) et un polissage aux oxydes (silice colloïdale, OP-U).
- Pour révéler davantage de détails ou des données plus spécifiques dans les structures en aluminium, les méthodes d’attaque chimique, électrochimique et optique peuvent être utilisées (ou bien ou une combinaison de ces méthodes).
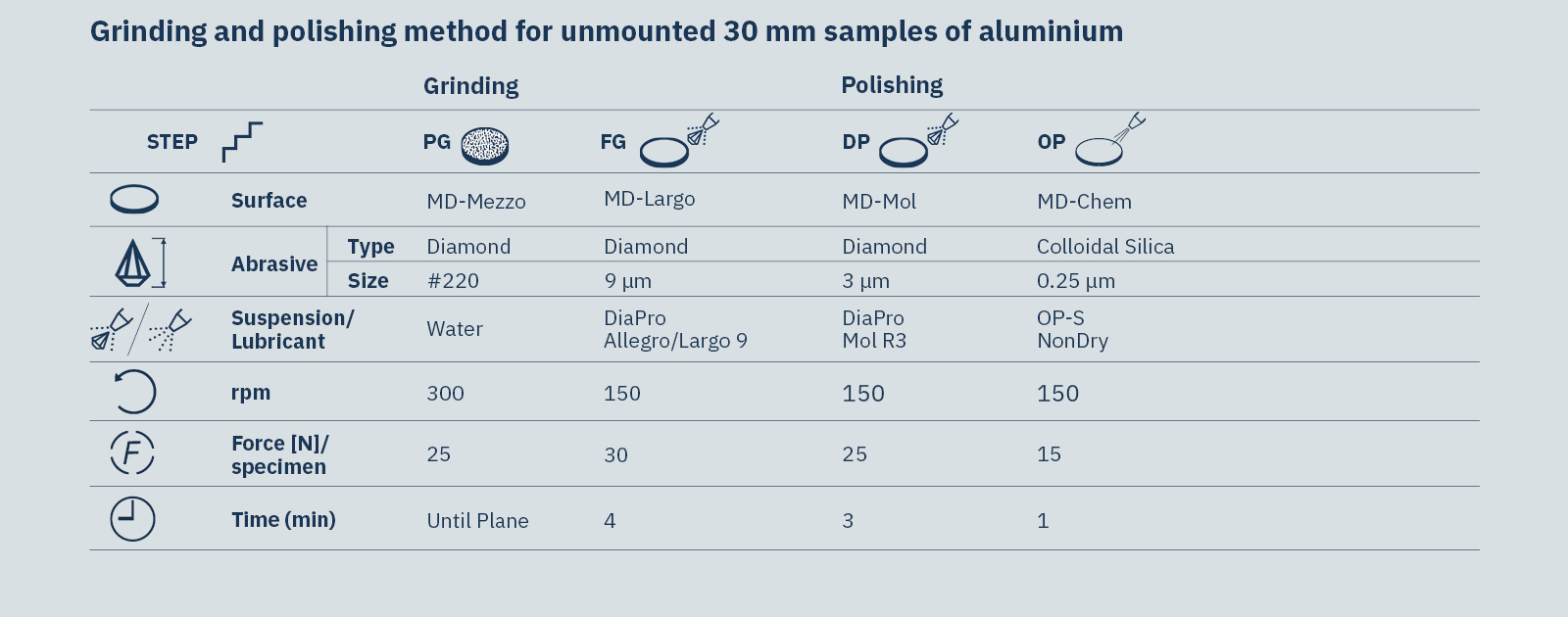
Tableau 3. Méthode de prépolissage et de polissage pour échantillons d’aluminium de 30 mm sans extraction de l'enrobage de son moule
Pour des informations et une méthodologie plus détaillées, consultez la note d’application complète.
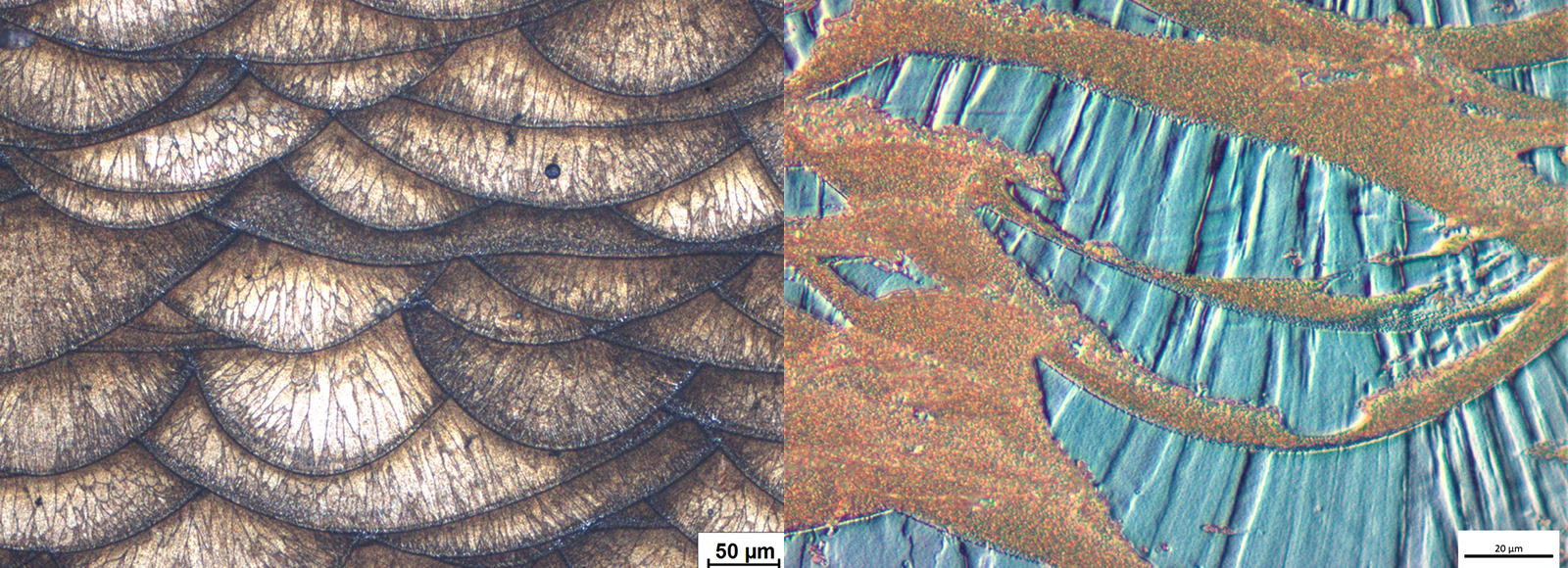
Figure 18. Différents alliages d’aluminium après attaque par réactif de Barker en fond clair (à gauche) et contraste interférentiel, DIC, (à droite).
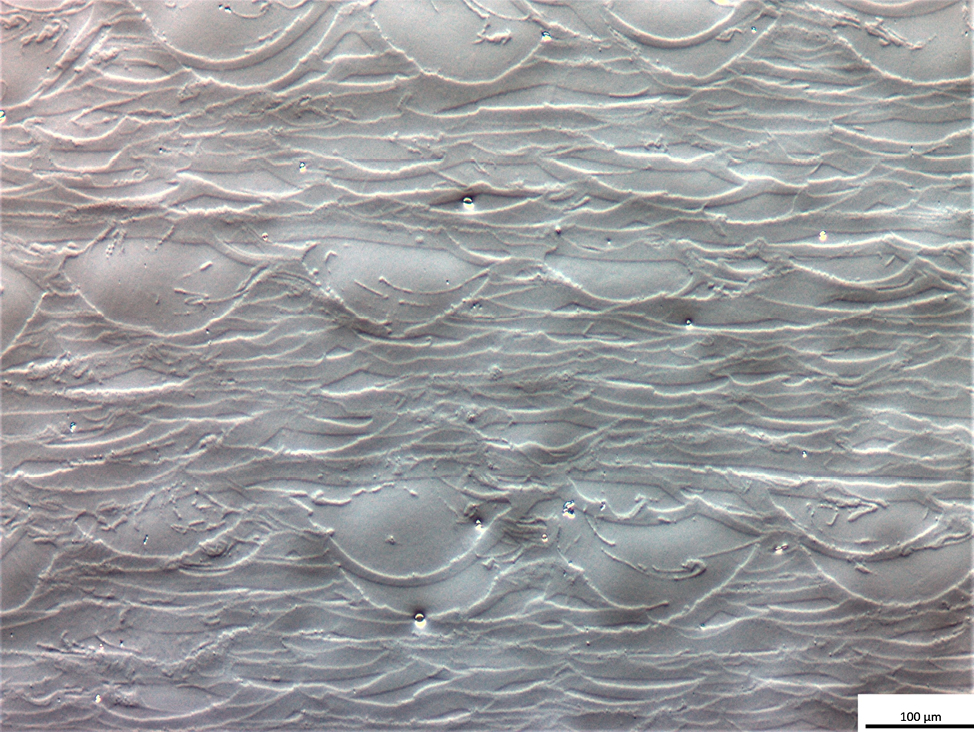
Figure 19. Surface avec polissage fin d’alliage d’aluminium. Polissage avec MD-Chem et OP-S. Contraste interférentiel, DIC, non attaqué.
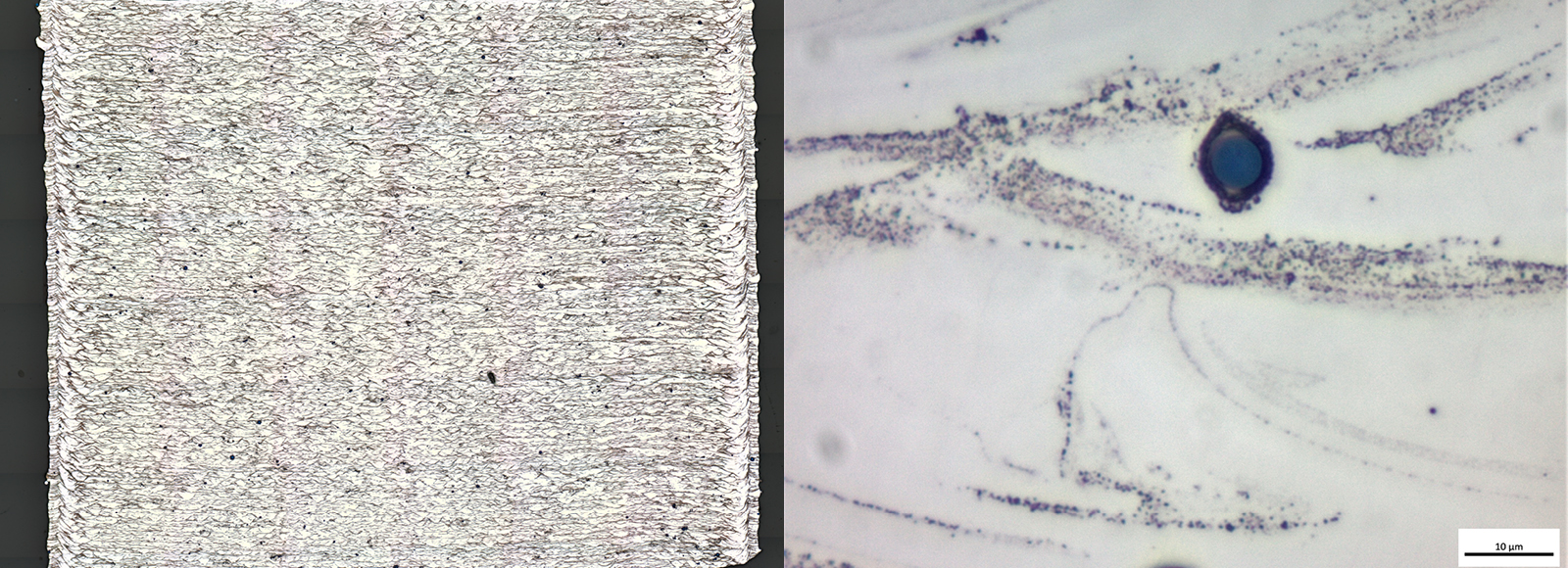
Figure 21. Vue d’ensemble d'un alliage d’aluminium, attaque avec réactif de Barker (à gauche). Vue détaillée de l’alliage d’aluminium, avec précipitation à fort grossissement (à droite). Fond clair.
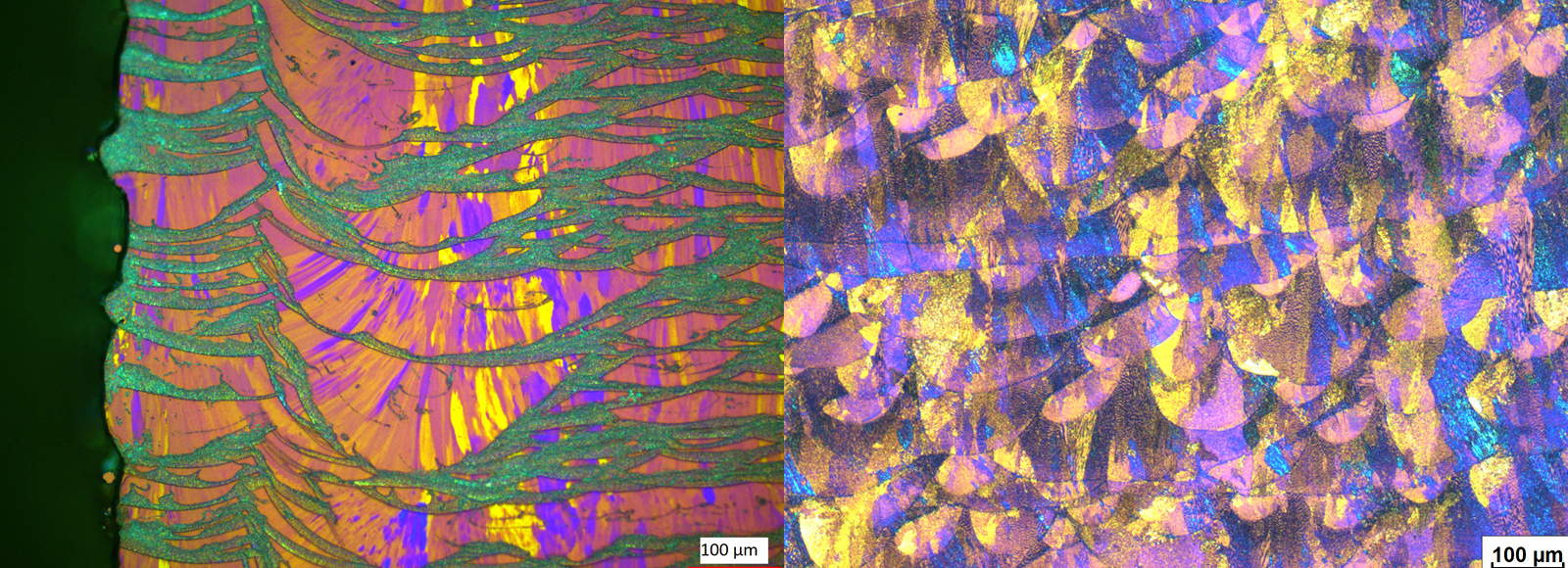
Figure 22. Alliage d’aluminium après attaque par réactif de Barker (à gauche). Attaque Inconel avec Adler (à droite). Lumière polarisée.
Aciers inoxydables et alliages à base de nickel Étant donné que ces matériaux sont souvent mous et ductiles, il convient d’éviter les surfaces de prépolissage très grossières et les supports haute pression. En général, la préparation doit suivre les méthodes standard utilisées pour les autres aciers inoxydables et alliages à base de nickel.
- Utilisez un disque de prépolissage plan dédié, tel que MD-Alto.
- Le prépolissage fin doit être effectué avec une suspension diamantée sur un disque rigide (MD-Largo) ou un chiffon MD-Plan.
- Procédez ensuite à un prépolissage fin avec un polissage diamanté complet sur un chiffon moyen/dur (MD-Dac).
- Nous recommandons un polissage final avec de la silice colloïdale (OP-S) ou de l’alumine (OP-A) pour éliminer les rayures fines.
- L’attaque électrolytique avec 10 % d’acide oxalique dans l’eau est courante. Pour les aciers duplex, l’attaque électrolytique avec du NaOH (20 % dans l’eau) donne de bons résultats.
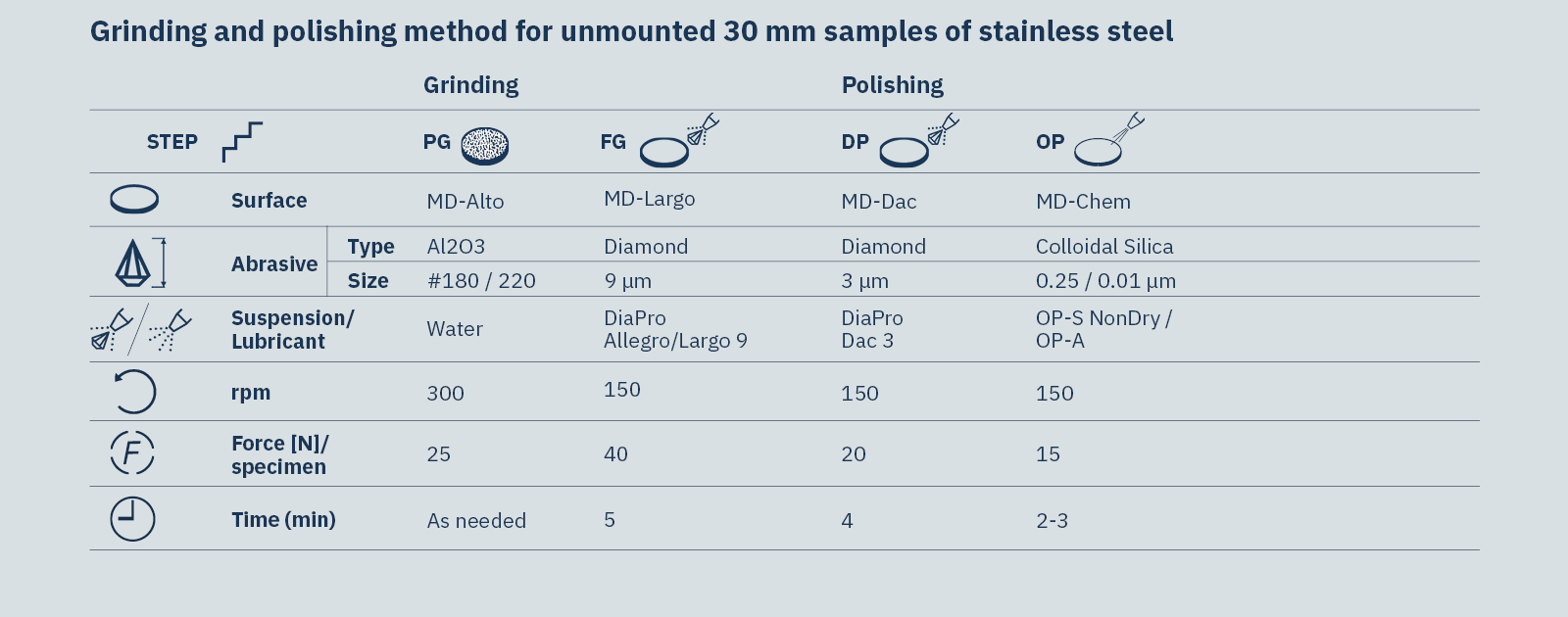
Tableau 4. Méthode de prépolissage et de polissage pour échantillons d’acier inoxydable de 30 mm sans extraction de l'enrobage de son moule
Pour des informations et une méthodologie plus détaillées, y compris la préparation d’échantillons pour l’évaluation de la porosité, voir la note d’application complète.
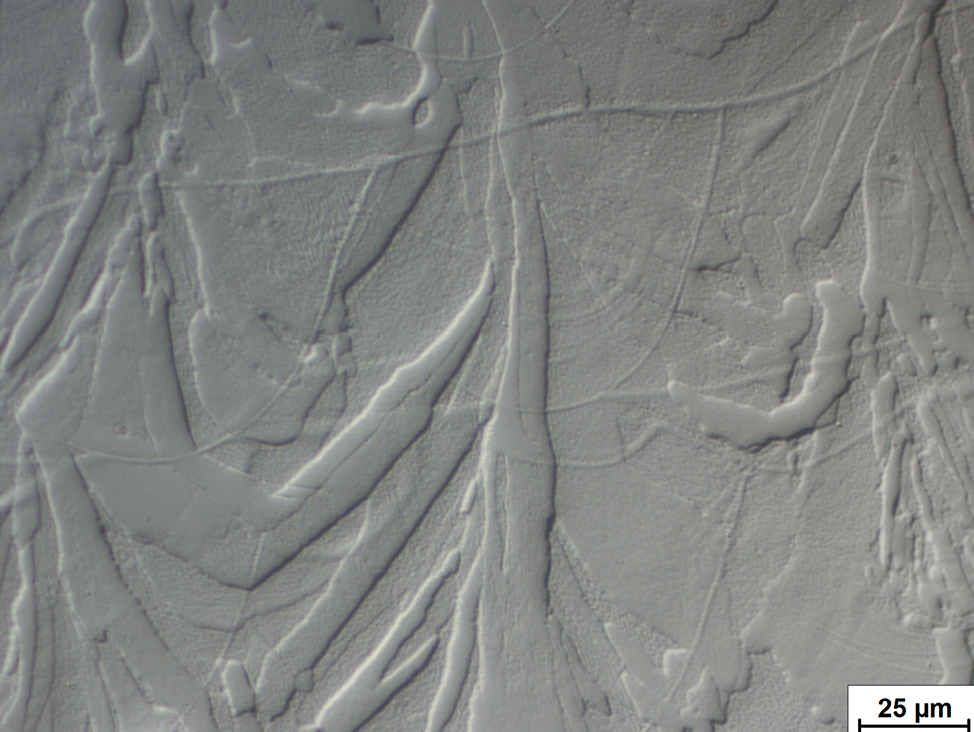
Figure 24. Acier austénitique après polissage avec OP-S sur MD-Chem. Structure visible sans attaque chimique. Contraste interférentiel, DIC.
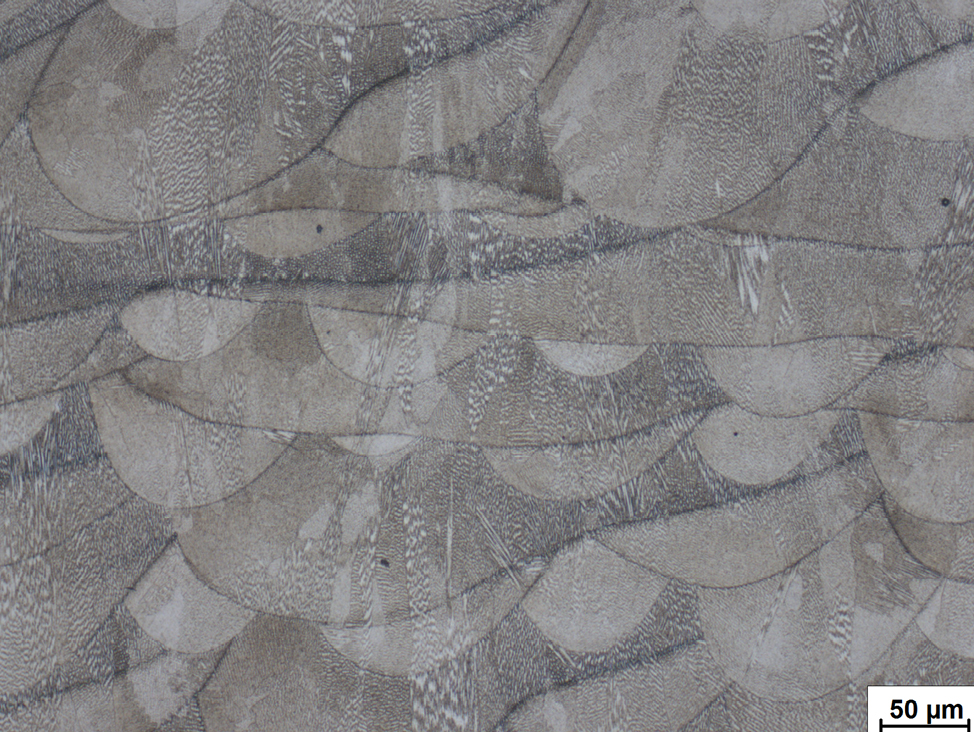
Figure 25. Inconel 718, attaque avec réactif d’Adler. Fond clair.
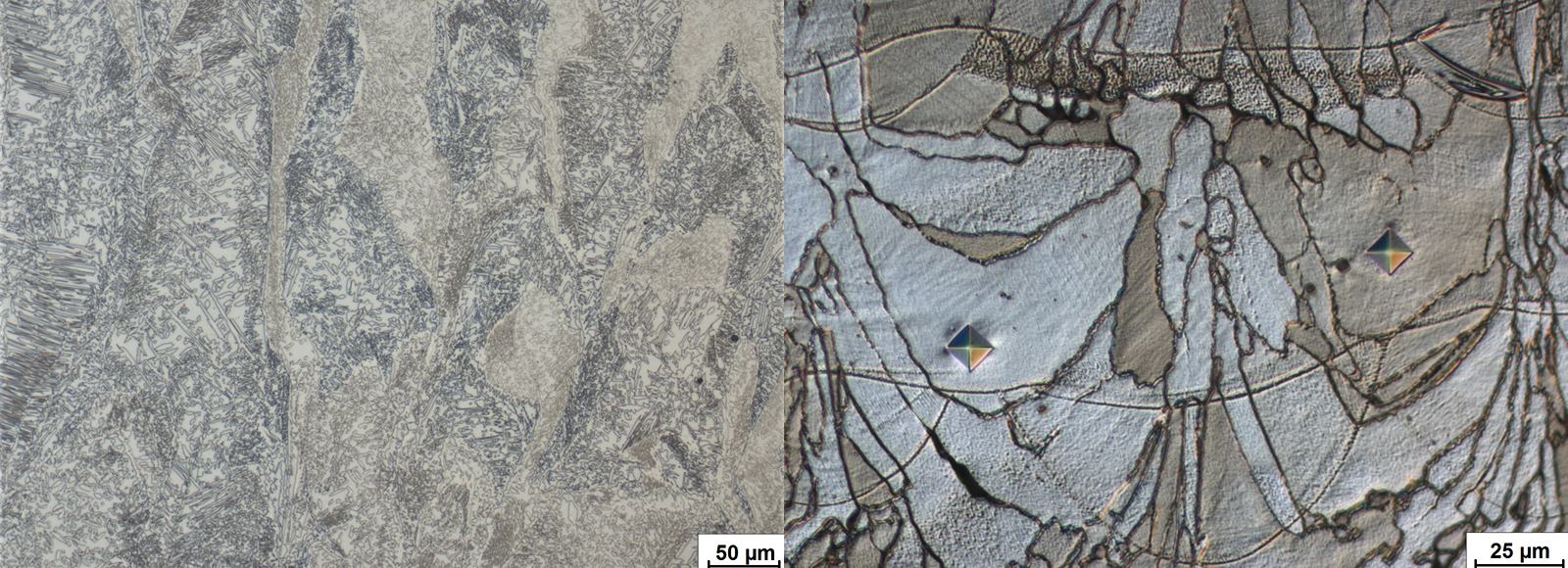
Figure 26. Acier duplex 1.4462 après attaque électrolytique avec acide oxalique (10 %). Fond clair (a gauche). acier duplex avec microempreintes de dureté, après attaque électrolytique avec 20 % de NaOH dans l’eau. Contraste interférentiel, DIC (à droite). Aciers à outils Les aciers à outils sont des aciers fortement alliés contenant de grandes quantités d’éléments d’alliage tels que le chrome, le nickel, le vanadium, le tungstène ou le molybdène. La principale difficulté lors du prépolissage et du polissage des aciers à outils fortement alliés est de veiller à la préservation des carbures et des inclusions non métalliques. En général, la préparation doit suivre les méthodes standard utilisées pour les autres aciers à outils.
- Pour le prépolissage plan, il est recommandé d’utiliser des disques de prépolissage plan avec diamants intégrés (MD-Piano).
- Pour un prépolissage fin, utilisez un disque diamanté à liant métallique (MD-Allegro) avec suspension diamantée.
- Pour les aciers fortement alliés, il est possible d’utiliser le réactif d’attaque Klemm.
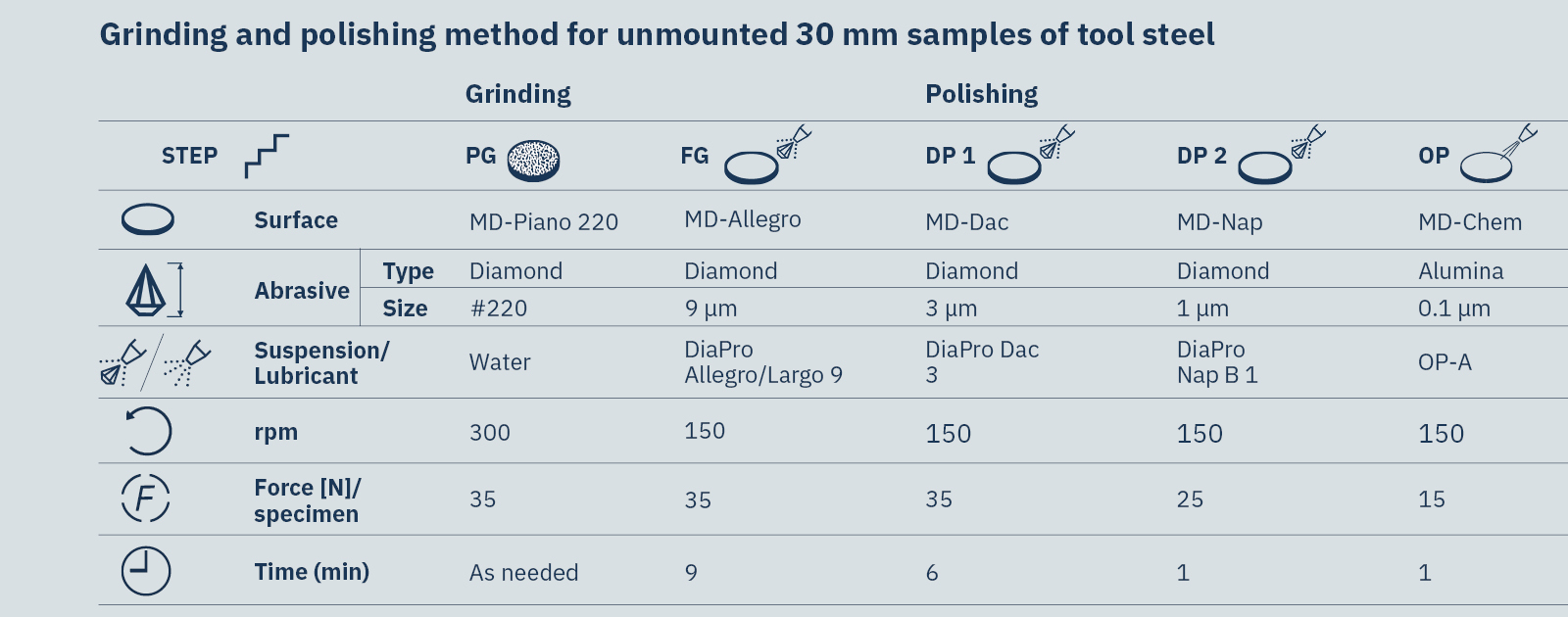
Tableau 5. Méthode de prépolissage et de polissage pour échantillons d’acier à outils de 30 mm sans extraction de l'enrobage de son moule
Consultez la note d’application complète pour obtenir des informations et une méthodologie plus détaillées.
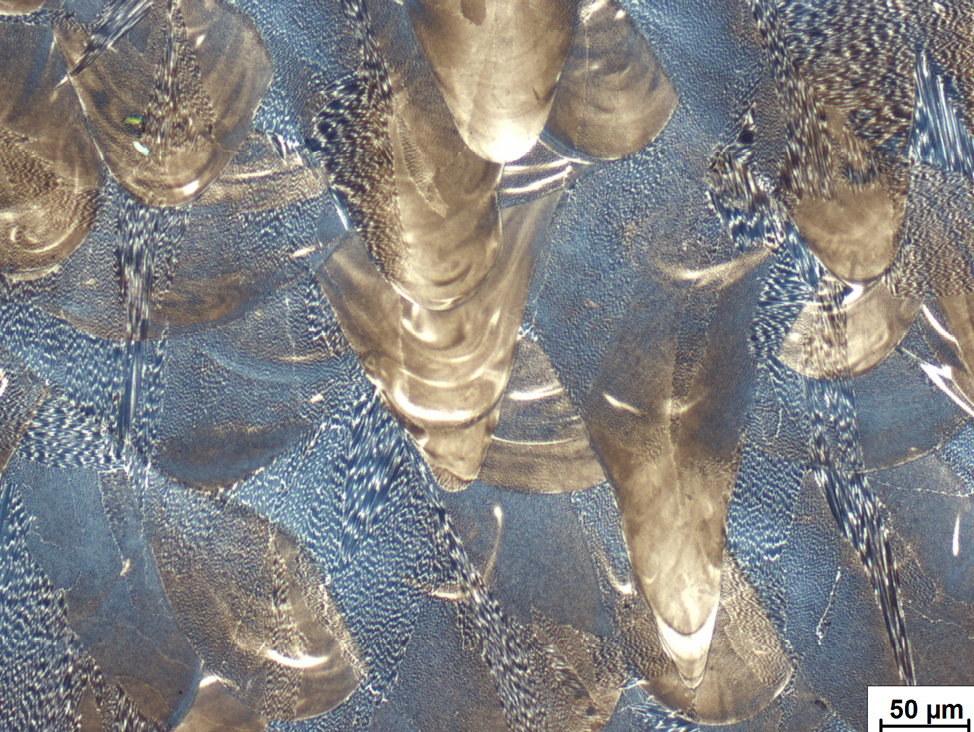
Figure 27. Acier à outils 1.2709 après attaque avec réactif de Klemm modifié (10/3) et ajout de HCl. En savoir plus